An Alumnus’ Take on the Coronavirus’ Supply Chain Impact
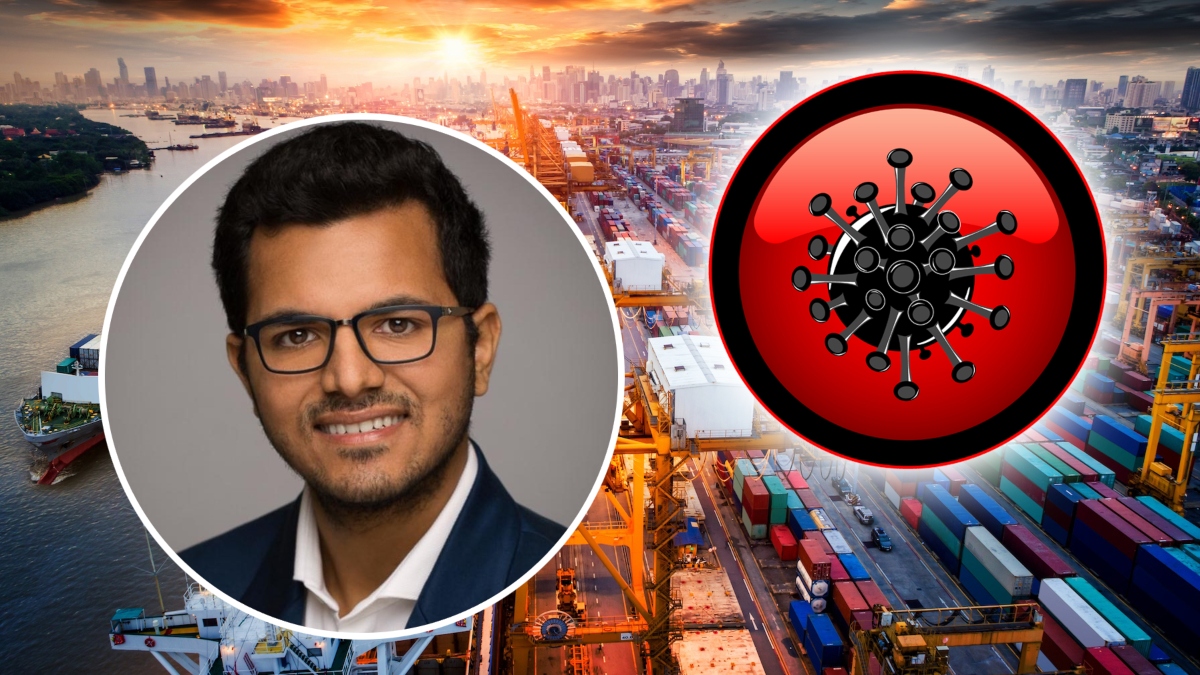
Krunal Sonpal graduated from NC State University in 2018 with a Master of Industrial and Systems Engineering degree and now works as VP of Sourcing at BNY Mellon. Since graduation, Krunal has been using data to see the impact of geopolitical, natural and man-made disasters on complex supply chains, and researching methodologies to reduce their overall effects. His areas of expertise include data analysis, contract negotiations and supply chain management. In the following article, Krunal shares his perspective on the impact of the recent coronavirus outbreak on the global supply chain.
Impact of Coronavirus on Supply Chain
by Krunal Sonpal
Superbugs that resist treatments and spread rapidly like the coronavirus always catch the headlines. As of Wednesday (02/19), the disease has affected 75,309 people and has surpassed 2000 deaths, higher than the SARS outbreak of 2002-03. With a mortality rate of ~2.5%, it’s not the deadliest virus; however, it is said that each person infected is passing the disease on to another two or three people on average, making it more contagious than the previous SARS outbreak. This has led to a complete shutdown in the city of Wuhan, the epicenter of the virus and one of China’s largest manufacturing centers.
Wuhan houses operations for more than 300 of the top 500 companies in the world including Apple, Microsoft, Dell, GM, Honda and BMW. The Hubei province, where Wuhan is located, is roughly half the size of the state of California but has a GDP of $600 billion in 2018- almost that of London and roughly same as that of Sweden and Taiwan.
Though we have already started to see some effects of the virus on supply chains, the full impact will become obvious in the next couple of months. Some of the areas where organizations will start feeling the impacts on supply chains include:
- Labor: With more than 60 million people put under quarantine, it will be difficult for manufactures to find enough laborers to meet the manufacturing requirements. Most multinational companies have either asked their employees in China to work from home from home and companies including BNY Mellon, Amazon, Google and Facebook have even limited employee travel to China and Hong Kong.
- Material: Unavailability of labor will have a direct impact on the shortage in supplies of material. In a world of “Just-in-Time” inventory management, there will be an acute shortage of parts manufactured in China. Hyundai already stalled its South Korean production of cars as it ran out of Chinese parts. A number of US automobile manufacturers estimate they are three to four weeks away from running out of parts as well.
- Sourcing and Logistics: Wuhan is a land-locked province and is best accessible through air. With nearly all airlines cancelling their flights to Wuhan and China in general, even if materials are available, they will still be stuck in the warehouses. Wuhan has major automobile, semiconductor and steel manufacturing industries. If companies were making clothes or sneakers in the region, they could set up manufacturing at alternative plants in other unaffected South East Asian countries, however, typical automobile fabrication plants costs upwards of $1 billion to open and it isn’t a financially viable decision in short-term.
- Demand: Retailers saw a 50% drop in traffic as Chinese New Year plans got cancelled. Consumers have become more cautious with fears about being in public and potential exposure to virus. Pete Seurken, President of RTi Global, a leading consultation firm in the resin industry said, “Overall demand for commodity resin used in all kinds of industrial applications was weak without the headwind of Coronavirus. However, we are now seeing much deeper demand destruction driven by the virus. Prices had slightly recovered from 10 year low but now it looks like we’ll retest those levels.”
- Industry Effects: The impact on the supply chain may also come in waves. As noted by a former senior Lenovo executive: “The impact of coronavirus on supply shortages is going to be felt almost immediately for the electronics sector, as they have a lot of JIT shipments, and use a lot of airfreight for valuable inventory. We are already seeing that Apple is taking a hit, and I believe other electronic manufacturers will as well. I think that retail and consumer goods will feel the impact, in 3 to 6 months, as they have more material in the pipeline, use more ocean freight with inventory on the water, and have more in their warehouses. But it is going to hit them eventually.”
Takeaways:
This sudden outbreak is a wake-up call for supply chain and procurement teams throughout the world. Companies need to pay closer attention to risks and resiliencies while designing their supply chains. They need to brainstorm and develop business continuity plans for potential disruptors including natural disasters, pandemics, war, tariffs etc. It is important to geographically diversify suppliers and find alternatives for high-end manufacturing.
Today’s supply chains took decades of R&D to optimize. It is crucial for China to demonstrate its ability to get its supply chain back online. Once the disease is brought under control and the crisis are mitigated, it would be important to forecast the next “when”.
- Categories: